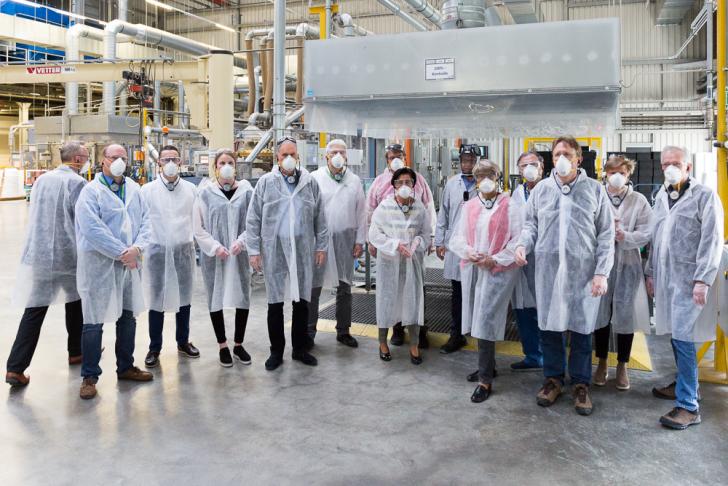
Der Besuch des Presse Club Hannover im Headquarter von Johnson Controls Power Solutions EMEA in Stöcken am 17. April 2018 war ein Einblick in Superlative: Man konnte die modernste Halle der gesamten Johnson-Welt bestaunen, bekam das vorbildliche Recycling-Programm des Konzerns vor Augen geführt und konnte lernen, dass Johnson Controls als „Best Place to Learn“ ausgezeichnet wurde. Nicht nur auf das firmeneigene Duale Studium, sondern auch auf die anspruchsvollen Ausbildungsprogramme und darüber hinaus die erfolgreiche Beschäftigung der ersten syrischen Mitarbeiter ist man sehr stolz.
Johnson Controls ist der weltweit größte Hersteller von Starter-Batterien für Pkws, Nutz- und Hybridfahrzeuge. Was nicht jeder weiß: Johnson Controls ist auch ein führender Anbieter von Technik, Steuerungen und Serviceleistungen zur Heizung, Lüftung, Klimatisierung und Kühlung sowie von Sicherheitssystemen. Insgesamt macht der Konzern mit 120.000 Mitarbeitern weltweit einen Umsatz von knapp 40 Milliarden US-Dollar.
In den Batterie-Standort Hannover hat der Konzern, dessen Zentrale und Produktion für Europa, den Nahen Osten und Afrika (EMEA) am Mittellandkanal steht, in den letzten fünf Jahren 110 Mio. Euro investiert – zusätzlich zum regulären Investitionsvolumen. Damit ist er die zentrale Produktionsstätte für Start-Stopp-Batterien in Europa. Seit Übernahme des Varta-Kernstücks 2002 wurden am Standort die Produktionskapazitäten vervierfacht bei etwa gleichgebliebener Anzahl von rund 1.300 Mitarbeitern. Auch die Europäische Entwicklungszentrale für die Johnson Controls Batterietechnik ist hier angesiedelt.
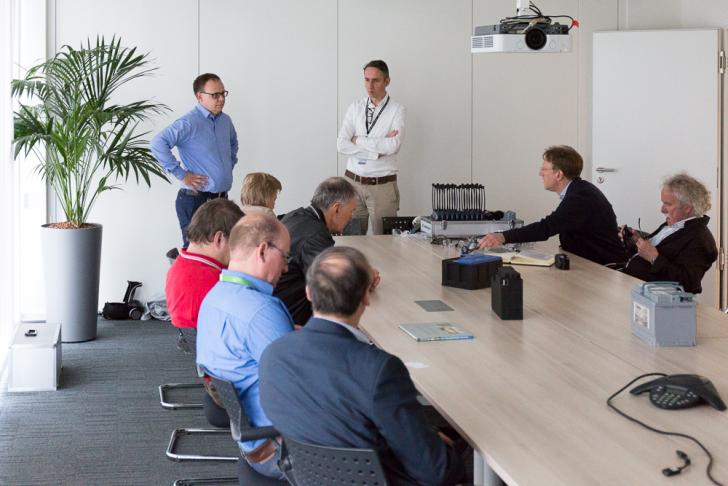

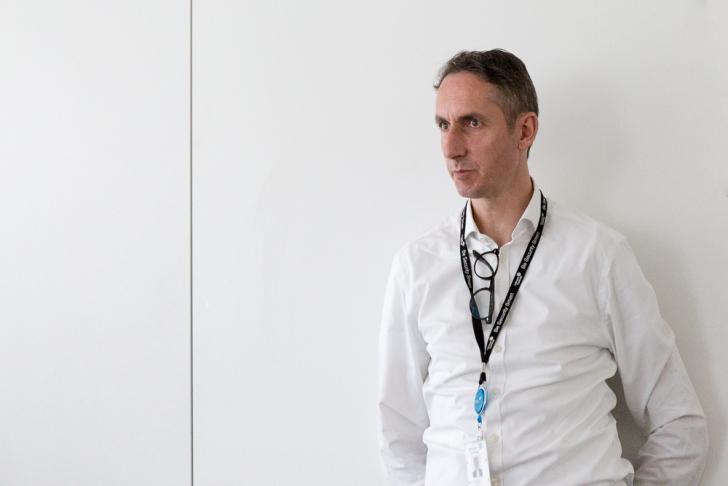
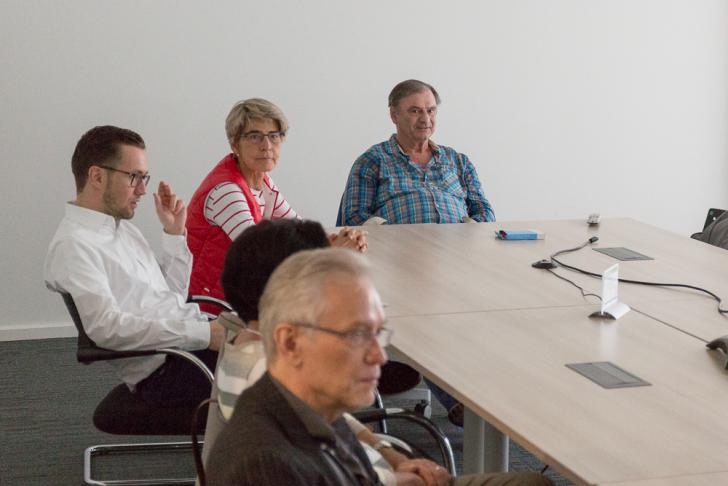
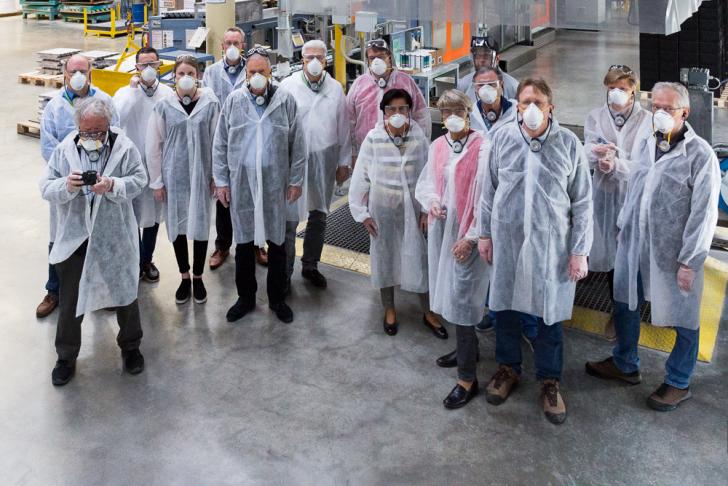
Werkleiter Jens Gehle und Christian Riedel, Director Communications EMEA, beantworteten auch die speziellsten Fragen der anwesenden 20 Presse-Club-Mitglieder sehr gewissenhaft. Am Schluss der überaus informativen Veranstaltung schwirrte allen der Kopf vor lauter Abkürzungen und Fachbegriffen wie Powerframe, Streckmetall, Oxyd, Curing, AGM, EFT und vielen anderen mehr. Die im Produktionsbereich verpflichtend vorgeschriebene Schutzausrüstung mit Atemmaske, Gummihandschuhen, Schutzbrille und Kittel tat bei sommerlichen 25 Grad Außentemperatur ihr Übriges.
Bericht: Nikola Meyerhoff
Fotos: Torsten Hamacher